
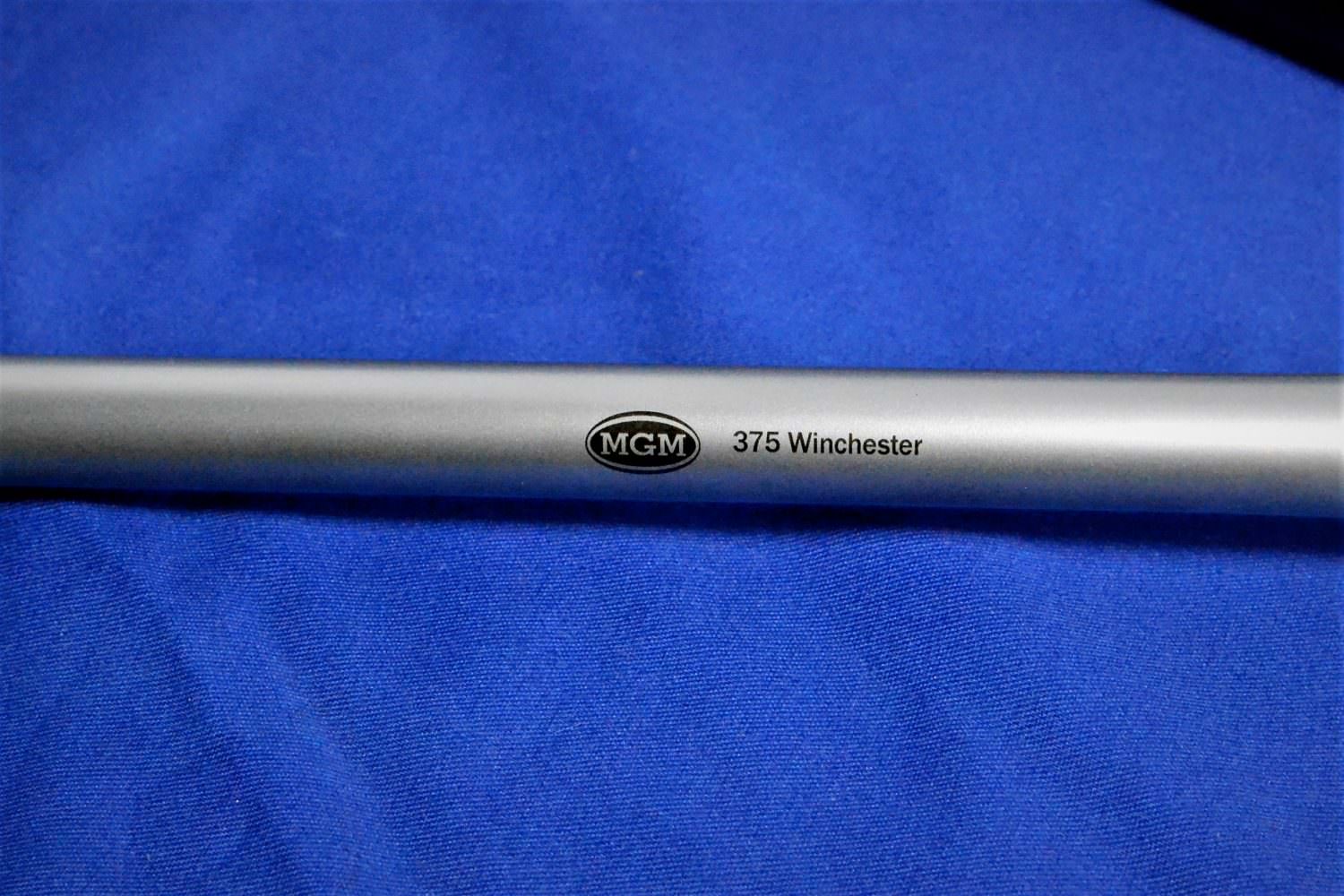
5mm thick, sufficent for all Wear and tear Purposes.Īfter WW I, they developed the "Kasenit" process, using Ferric Cyanate ( a Prussic Acid derivative), which simply required the red hot article to be dipped into the Powder, and then further heat treated. This left a Layer of hardening ( don't ask me about the metallurgical terms) from. When they were done, they were then cooled to get the "hardness" this hardness was then "drawn" to get the correct level, by re-heating, but to a lower level, so that the steel was not Brittle. the Parts were packed into a Iron case or box, with powdered Bone charcoal, and heated up to carburising heat for several days. Originally the case hardening was exactly that. The Medium carbon steel takes a good "Case hardening" which is used to toughen up the wearing surfaces and the high pressure surfaces (Bolt heads, receiver locking shoulders, etc. SAE 1035 is what is commonly called "mild steel" or medium carbon steel ( Common construction and reo steel is 1020). The Closes US Equivalent ( mentioned in the 1930s and 50s, in several US texts) is SAE 1035 for General parts, and 1085 for springs ( both flat and coil).
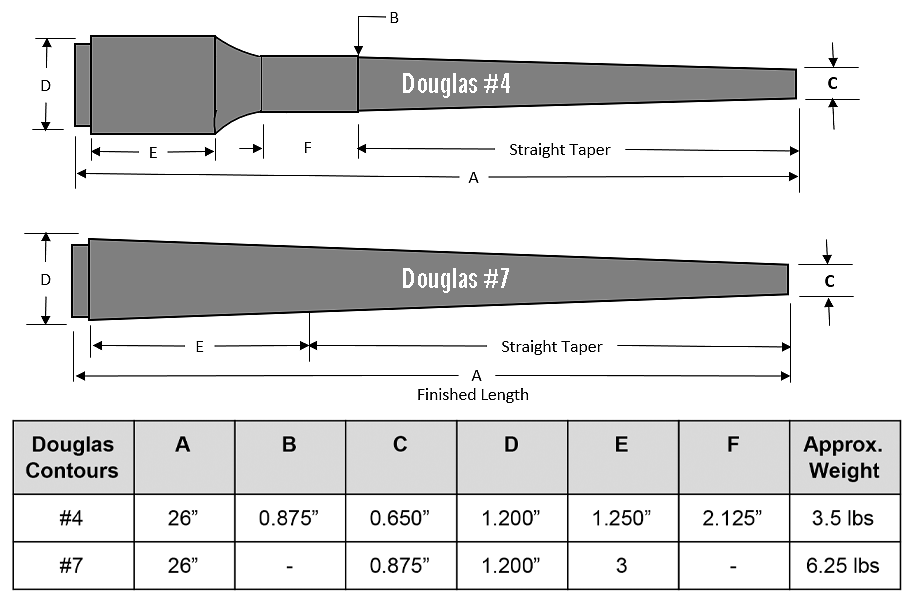
The germans tended to use two basic steel compositions, one for general parts, and another for springs. They can give you a relative indication of heat treat/metal hardness but they cannot tell you how the heat treat was done.Įach Country had its own "particular" method for selecting Gun steel. Even there they can only tell you percentages of ingredients and comment on metal grain structure. Someone may be more definitve on who and when on these points but I think I have the general idea right.ĭefinitive analysis of No.1 barrel steel would require destruction of barrels and testing in a Metalurgy lab. This system has become universal with the latest challenger being the rotary hammer forged barrel where the barrel is hammered down over a fully rifled/chambered mandrel. As you can imagine the broach was expensive to make and wore out quickly so they developed the button rifle broach where the broach was revised to take a small tungston carbide cutter (the button) what was cheaper and quicker to make to cut the rifling.
GUN BARREL STEEL GRADES FULL SIZE
Was it one of Campbell's books on the O3 Springfield that said broach rifling was developed by Remington mid WWII? A fully rifled cutter tool (broach), starting out small and growning in stages to full size was pulled through the barrel in one go resulting in a fully rifled bore. You don't have to have an engineering background to appreciate and use this book. I strongly recommend Gogan's "Fighting Iron, A metals handbook for Arms Collectors." as he explains how the term mild steel has had so many different meanings over time-it is practically useless as a descriptive word. Even the Garand receiver was batch lot sensitive. Why not on No.1 and No.4? Perhaps some were more design sensitive. I believe the lack of quality control is why they were so fixated on recording steel batch numbers on the actual weapons (No.2 revolver and Martinis). Until the common acceptance of the US Society of Automotice Engineer's method of steel specifications in the (I am guessing about 1940) people really didn't know what alloying material went into some steels.īritish drawings I have had access all seem to refer to supplier trade names for materials (a practice not done in the US) or really ambiguous terminalogy such as mild or low carbon steel. One of these days I'd like to visit Douglas barrels in West Virginia and do a plant tour.a friend of mine took one and suggested I go.ĭifferent countries over time had different methods of calling out steel specifications. This could be done a lot quicker and if the barrel didn't meet inspections, it could be remelted. There's more time spent making the finished product.īut, I would think that during the war years of WW 2 that there were advances in technology that allowed for better grades of steel and the ability to make and fabricate a carbide button that could be swedged through the barrel, imprinting the grooves by force from the hydraulic rifling machine. Cut rifling demands more labor (honing the cutter, sharpening the cutter, polishing the cutter, raising the cutter, inpecting the cutter, inspecting the barrel, polishing the barrel, so forth and so on.). I would think that inthe early 1900' the technology to produce a variety of barrel steels (or steel for that matter) was limited compared to the metalurgy we have today.alloys we have today may not have existed during that time.Īs for the rifleing process, I would have to think that cut rifling using scrape cutters or hook cutters would have been used during this time as well.
